When to consider getting an automated packaging line? We are offering some of the most important reasons why this is a good route for your company.
Maybe you started from your home, enthusiastic but never thinking it would outgrow your capacities. When people became interested in your products, you hired somebody to help you. Soon, one team member turned into two, two to three… You all worked hard to create the best possible product and experience for your customers.
The result is extensive growth in demand.
In this case, you need to consider possible options to improve the efficiency of your processes. One way to achieve this goal is to implement packaging automation. When it becomes hard to fulfill the demand, it might be a good idea to consider automation of the packaging process.
Based on the experience with multiple businesses, our startup customers begin production with short-run packaging requirements — volume ranging from 5,000 to 20,000 units every 4 months.
Many choose the Roll End Front Tuck box. It works well as it provides a low cost for manufacturing, mainly because it doesn’t require gluing. RTE (Reverse Tuck End) Box is the standard style of boxes for retail packaging for smaller-sized products like mascara, eye-liner, toothpaste, etc.
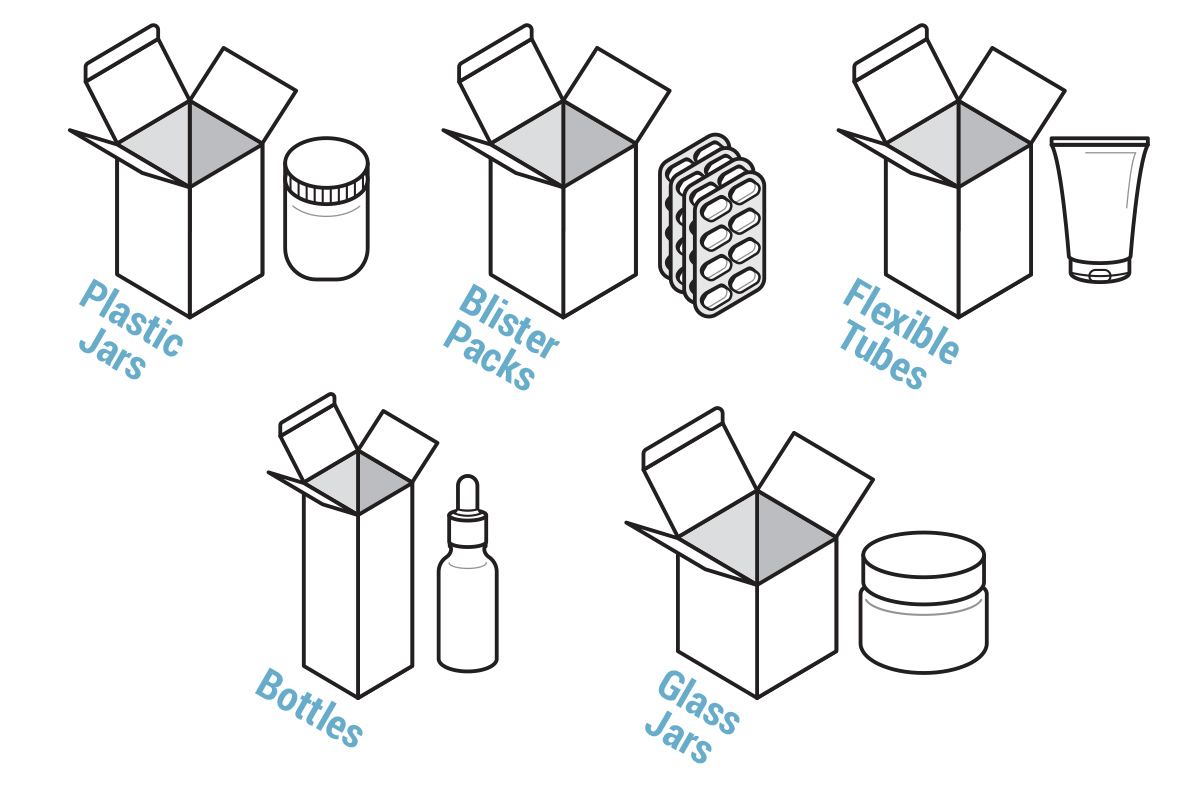
Although the labor cost is on the higher end, the material cost is on the lower.
This means the production needs to become more efficient. The best way to achieve that goal is by implementing automation.
Over time the volume and demand increase. It goes from 5,000 to 20,000 they start with, to 300,000 every 4 months.
Quantity | 1,000 | 2,500 | 5,000 | 10,000 | 25,000 | 50,000 | 100,000 | 200,000 |
---|---|---|---|---|---|---|---|---|
Cost Per Unit Printing | $0.50 | $0.40 | $0.35 | $0.30 | $0.20 | $0.10 | $0.08 | $0.07 |
Total | $500 | $1,000 | $1,750 | $3,000 | $5,000 | $5,000 | $8,000 | $13,000 |
Cost/Unit Packaging Manually | $1.00 | $0.90 | $0.80 | $0.75 | $0.60 | $0.50 | $0.45 | $0.40 |
Total | $1,000 | $2,250 | $4,000 | $7,500 | $15,000 | $25,000 | $45,000 | $80,000 |
Cost/Unit Packaging Automatically | $3.00 | $2.50 | $2.00 | $1.00 | $0.50 | $0.25 | $0.10 | $0.06 |
Total | $3,000 | $6,250 | $10,000 | $10,000 | $12,500 | $12,500 | $10,000 | $12,000 |
The numbers and calculations presented in our tables are based on our surveys collected from various co-packing production facilities.
Cost of Packaging by Efficiency:
Quantity | 1,000 | 2,500 | 5,000 | 10,000 | 25,000 | 50,000 | 100,000 | 200,000 |
---|---|---|---|---|---|---|---|---|
Manual Cartoning | 300.00% | 277.78% | 250.00% | 133.33% | 83.33% | 50.00% | 22.22% | 15.00% |
Automatic Cartoning | 33.33% | 36.00% | 40.00% | 75.00% | 120.00% | 200.00% | 450.00% | 666.67% |
Cost Per Unit Printing | $0.50 | $0.40 | $0.35 | $0.30 | $0.20 | $0.10 | $0.08 | $0.07 |
Total | $500 | $1,000 | $1,750 | $3,000 | $5,000 | $5,000 | $8,000 | $13,000 |
What is Cartoning Automation?
Packaging automation means packing the product without human assistance. These machines eliminate redundant tasks, allowing better use of your employees’ skills and time. You can choose the degree of automation that best suits your business. Some machines cover just part of your production process. These are a good option when you are beginning your automation journey. You can add the elements of automation as your business grows. Later, when your production reaches a level that is impossible to service manually, you can consider automating your production processes fully.
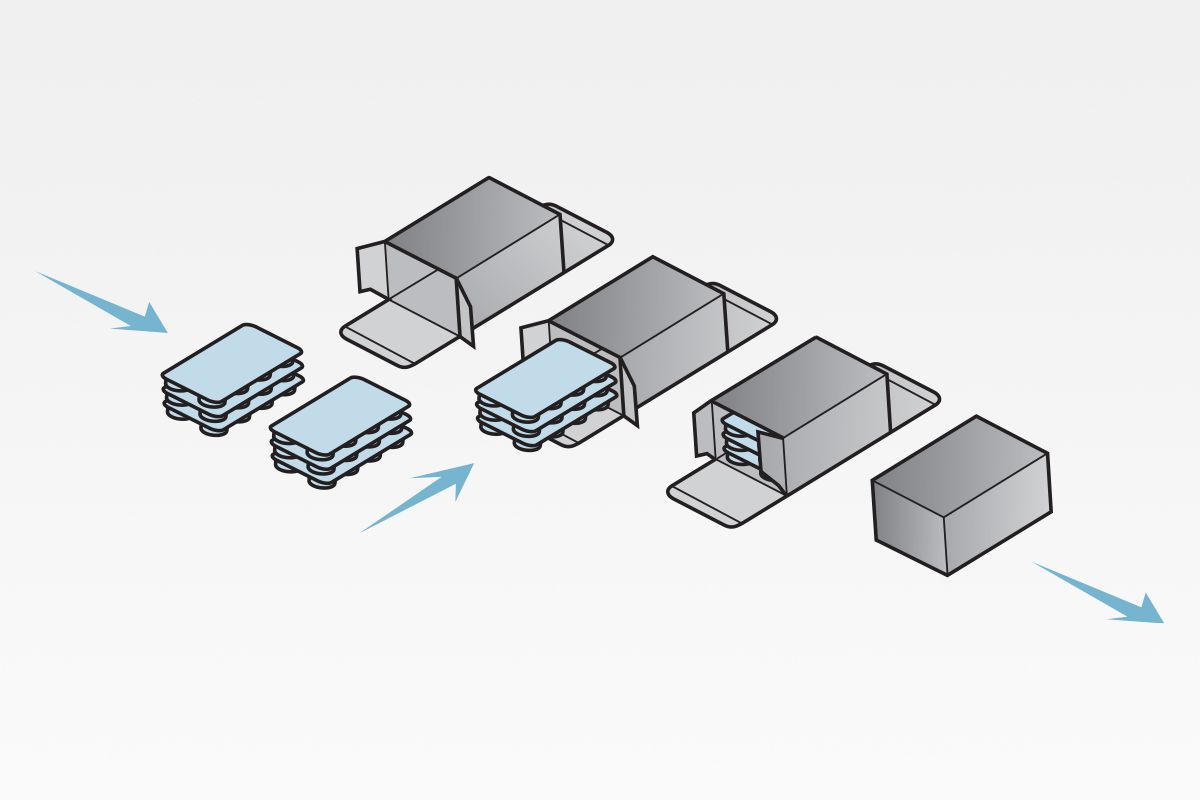
Reasons to Implement Cartoning Automation to Packaging
You Expect Your Business to Grow
Keeping up with demand is the most often mentioned reason for packaging automation. Production can’t achieve full growth potential unless the processes are automated to at least some level. Although your equipment and employees can support your current production level, you should prepare for the anticipated growth. Not being able to fulfill future orders would mean losing the customers you worked hard to get. Constantly hiring new people and training them leads to high-stress levels and an increased possibility of mistakes. It also increases the costs of the workforce. This brings us to our next reason for considering an automated packaging line.
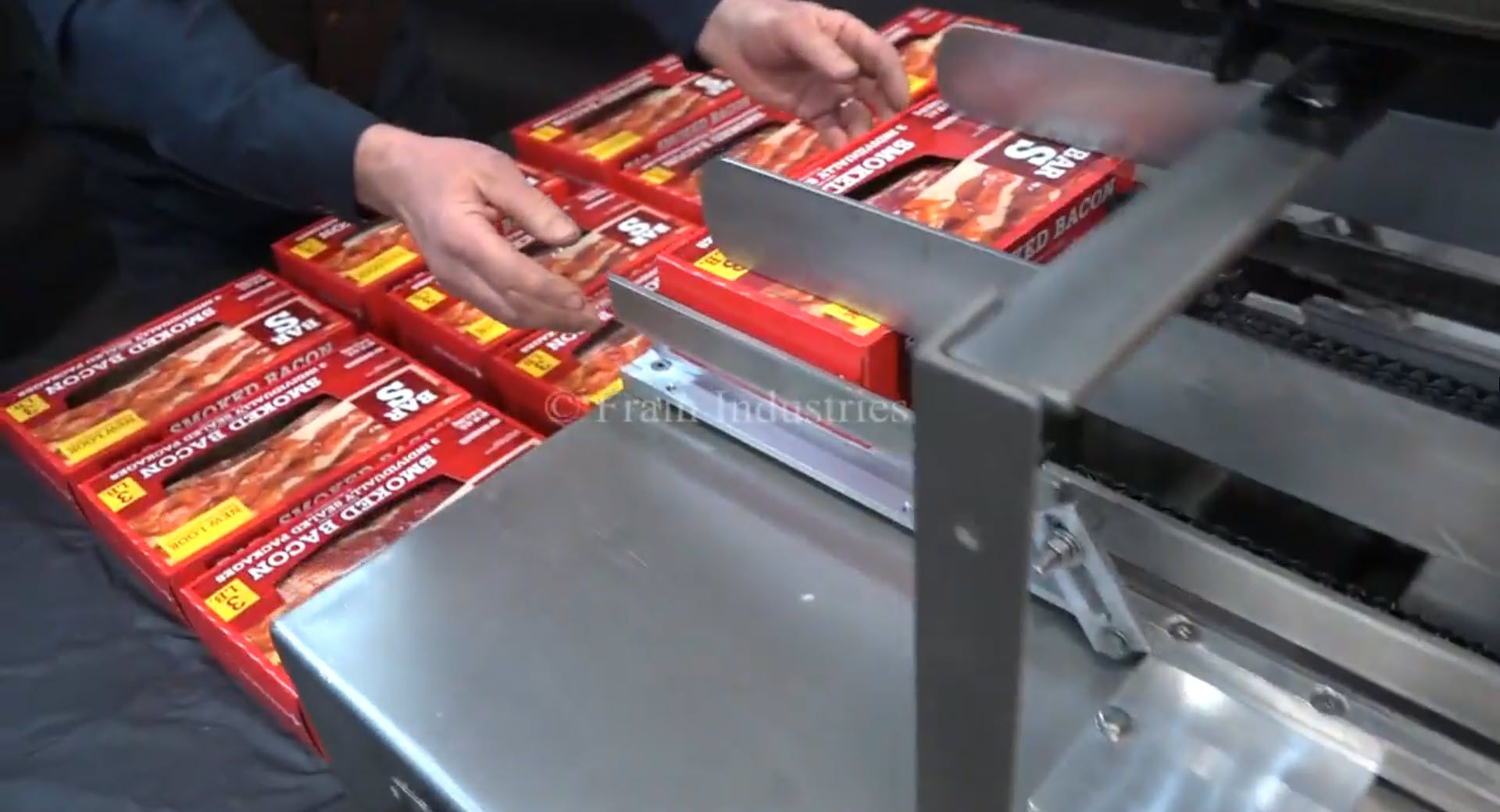
You have High Labor Costs
When considering labor costs, it is essential to ensure you also consider sick days and vacation time, not just hourly wages. Replacing your regular workforce with temporary workers further increases your labor costs. Also, somebody needs to train those new people. And having significant workforce fluctuations increase the number of beginner mistakes. Automated packaging equipment will probably pay for itself in one or two years with just labor savings.
Very often, only one person can operate this equipment. And you can train somebody else to jump in, if necessary, to ensure there are no delays due to a lack of operators. Automating your packaging lines means you will not have more workers in the packaging process than you actually need. However, this doesn’t mean you have to let go of your valuable employees. They can be trained and moved to other teams. Having more people in customer support is always a good idea. This will probably improve both team members and customer satisfaction. Which usually leads to more sales and higher profit.
Automation Means Lower Environmental Impact
Lowering the environmental impact of every process in the company is one of the main goals of modern businesses. Packaging automation solutions available on the market have lower emissions and use less energy than outdated machines. They need less maintenance and replacement parts than human-operated equipment. This way, your business will be one step closer to having fully sustainable packaging.
Also, automated systems are usually more precise than humans. Once set the right way, they don’t use more material than necessary for production and packaging. Manual labor produces more waste, and humans are prone to mistakes that lead to having to discard products and packaging. Machinery is precise and thus can help in packaging cost saving.
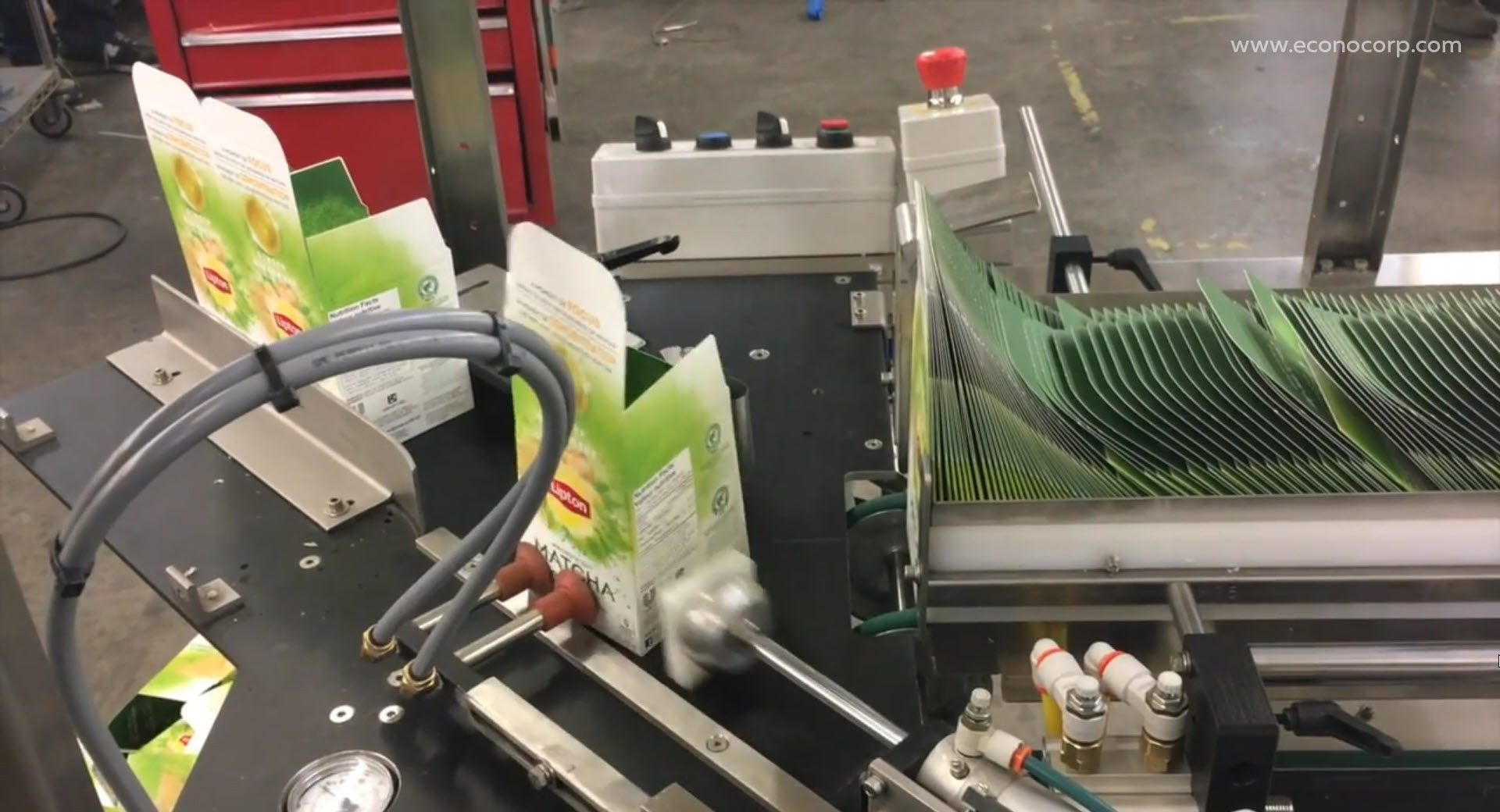
Simple and Repetitive Packaging
Automation is best implemented when there are repetitive and straightforward steps done repeatedly.
It might not be the best idea for uniquely shaped or bulky items.
However, even if your packaging is not the most suitable for automation, you may consider changing your packaging style.
RETF (Roll End Tuck Front) boxes are a prevalent choice for the manual packaging process. They look nice, there is no need to use glue, and they are easy to assemble. The downside is that it takes approximately two minutes to package the product. If you insist on using a RETF style of box, and your volume becomes recurring throughout the year, you may find equipment to automate the entire process.
If you are using RETF boxes but want to switch to packaging automation, changing the style of the box to 4 Corner Box can help you decrease the assembly per package by 75% (from two minutes to 30 seconds). Not only will the assembly time go down, but you will also have the box style suitable for automated packaging processes. The box itself represents the brand and the product and should be considered part of the product’s overall look.
Results of Packaging Automation
Automation Saves Money
Although implementing automated packaging solutions has high costs, the ROI (return on investment) is also high. So, investing in this equipment is usually a good idea. With packaging automation, companies are saving thousands of dollars in wages. They don’t need to hire people to do boring and repetitive tasks.
There is also the benefit of avoiding labor turnover costs and hiring mistakes usually involved with high workforce fluctuations.
These machines have a specific purpose and are designed so they don’t require much maintenance. Not many components break down easily, so the companies are saving on maintenance costs and spare parts.
As automated packaging equipment doesn’t tend to make mistakes and cause accidents, you will not have to pay for hospital bills. You will also spare your employees from having a traumatic workplace experience.
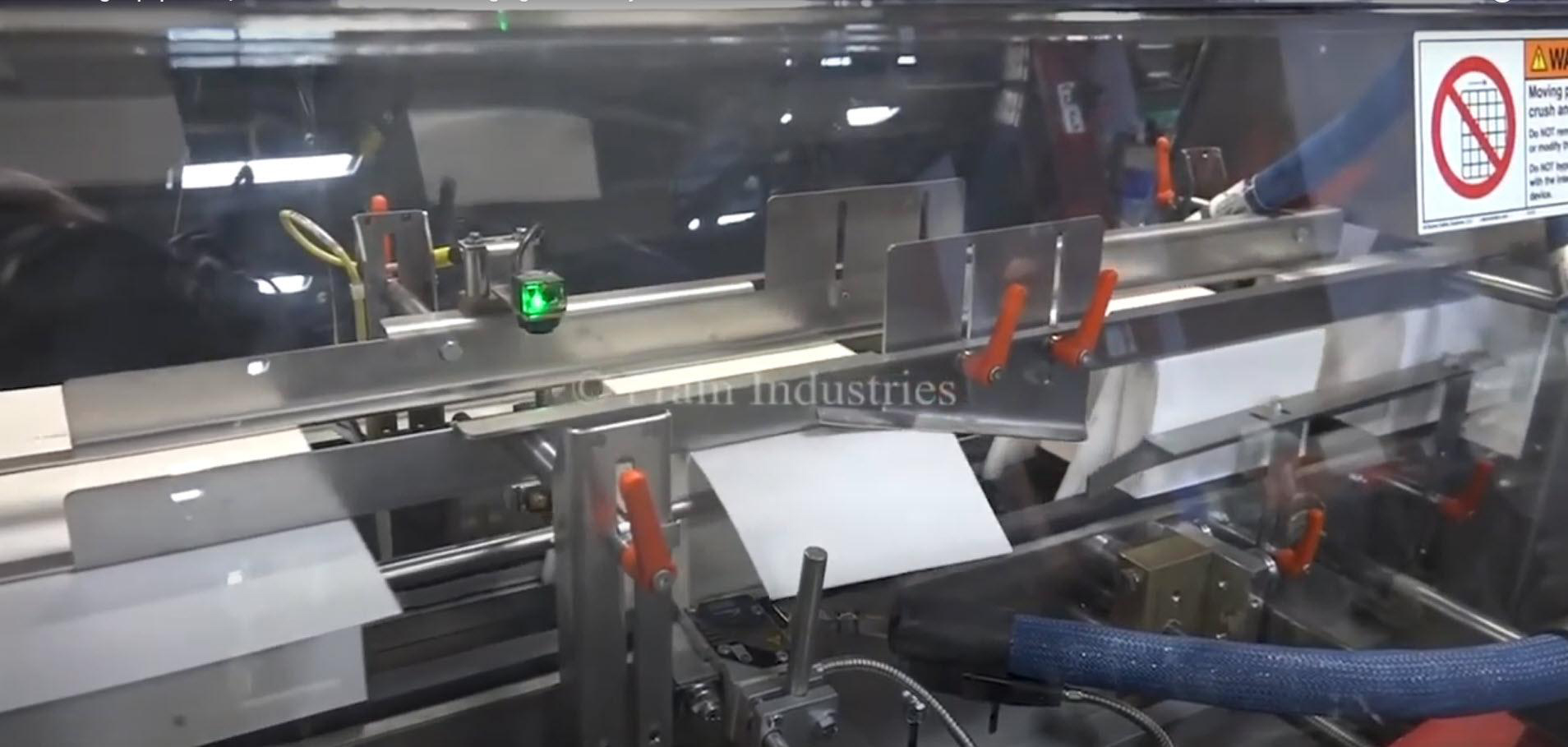
Automation Is Time Efficient
Machines work faster than humans. The processes will take much less time than when they are done manually. This leaves employees more time to focus on tasks that can’t be automated as efficiently.
Smoother workflow results in better quality control and helps avoid bottlenecks that can slow down productivity.
Quantity | 1,000 | 5,000 | 10,000 | 50,000 | 100,000 | ||
---|---|---|---|---|---|---|---|
Manual Labour | 100 | 102 | 104 | 106 | 108 | Per Hour | |
Semi-Automatic Machine | 200 | 1000 | 1500 | 2000 | 2500 | Per Hour | |
Full Automatic Machines | 200 | 1250 | 2000 | 3000 | 4000 | Per Hour | |
Total Time (Units/Time) | |||||||
Human | 10 | 49 | 96 | 471 | 926 | hours | |
Semi-Automatic Machine | 5 | 5 | 6.67 | 25 | 40 | hours | |
Full Automatic Machines | 5 | 4 | 5 | 16.67 | 25 | hours | |
Speed (vs Human) | |||||||
Semi-Automatic Machine vs Human | 2X | 10X | 16X | 18X | 23X | ||
Full Automatic Machines vs Human | 2X | 12X | 19X | 31X | 37X |
The right software can track processes and help simplify them by collecting available data throughout your company.
Automated packaging ensures a timely response to demand increases. It allows better use of human capital by taking over repetitive and straining tasks that can be hard for humans. It can also combine different parts of the packaging process into a single step (like sealing and labeling).
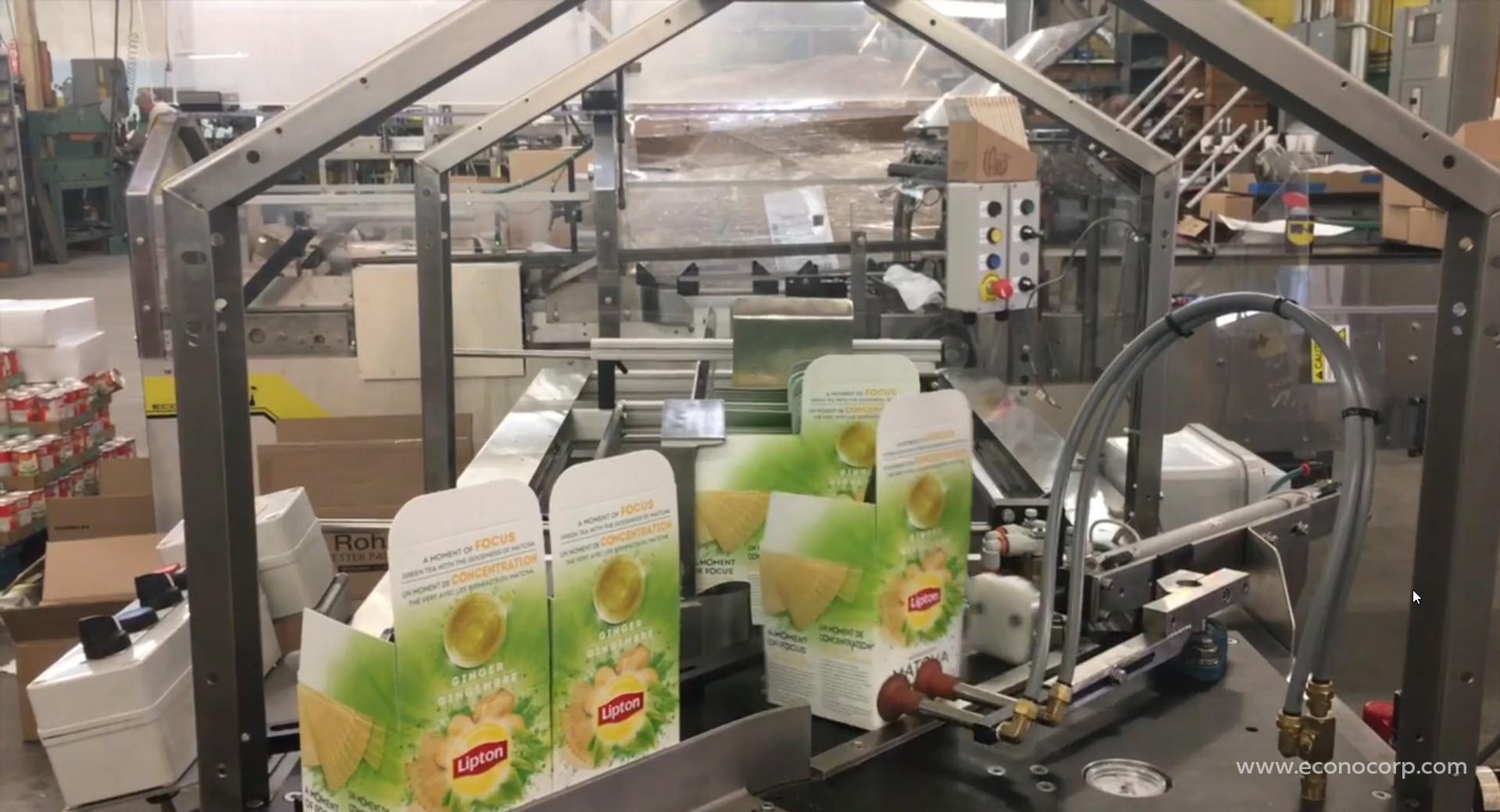
Automation Reduces Human Error
Packaging machines complete tasks more accurately than humans. They don’t get tired or unfocused when working long hours. It is impossible for humans to perform tasks exactly the same way every time. This creates variations that are undesirable in production processes. Automation ensures consistent results.
The development of new technologies using artificial intelligence allows computers to perform tasks like quality control more efficiently and consistently than humans.
Reduced possibility of errors and consistent pace on the packaging lines are increasing both productivity and profitability.
Better Customer Satisfaction
As automated systems are far less likely to make errors than humans, there is less chance for damaged products to get to customers. Both manual production and manual packaging process create a higher chance for products to be damaged. Automation means fewer returns, increased customer satisfaction, and fewer costs involved with returns.
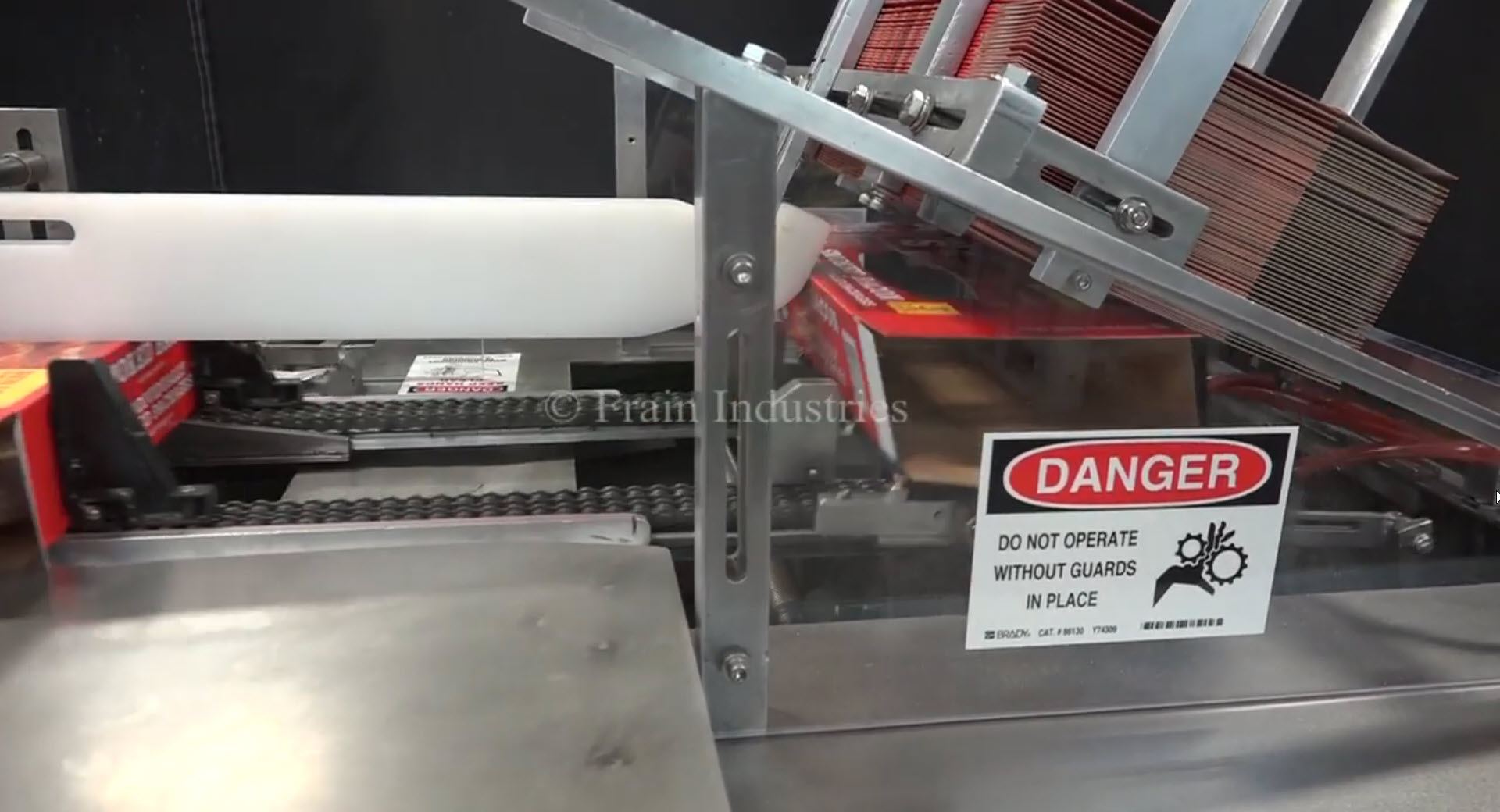
Improved Workplace Safety and Satisfaction
Repetitive motions increase the chance of workplace injuries. This can cause high costs of paid leave and disability. The reduction in compensation claims can justify automated packaging expenses.
Also, if your employees are more involved with creative work than simple repetitive tasks that machines can do, they will be more motivated to work. A healthy work environment and satisfied employees always help the company grow and develop.
The increase in volume doesn’t mean that the company needs to venture out and manufacture the product in China or other Asian countries. It only means that the North American brand needs to find a solution to reduce the labor-intensive processes and change them to automated processes.
There are many ways to reduce your overhead and increase your throughput. Just make sure to build a plan that will last.